3D Printers aren’t your dad’s daisy wheel or mom’s dot matrix, they build objects in three dimensions! They are now a regular fixture on shop floors, design studios, rec rooms and kitchen tables.
The technology is enabling product designers and engineers to test and validate products in a fraction of the time, speeding up time to market significantly. Visit Our Website to learn more.
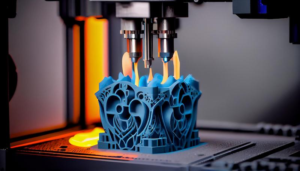
3D printing is an ideal tool for rapid prototyping, enabling designers to test and refine products without the time constraints that come with traditional manufacturing processes. By eliminating the need for costly tooling, product teams can make design changes in a matter of days, rather than months. This enables businesses to stay agile and responsive, and ensure that their designs meet customer requirements.
With a number of different printing technologies available, it’s important to choose the one that best meets your specific needs. Each has its own unique set of benefits and drawbacks, and some are better suited for certain types of prototyping than others.
FFF is a cost-effective and efficient printing technique that produces parts quickly. Its versatility makes it a great choice for creating functional prototypes, where the visual appearance of the finished product is secondary to its functionality. FFF printers are also easy to use, and can print a range of thermoplastic materials.
DLP and SLA are both effective prototyping techniques that produce high-quality models with intricate details and a smooth finish. They are also able to create complex shapes and can accommodate a wide range of material options, including metals. However, DLP and SLA printing methods can be more brittle than FDM, and their support structures may leave blemishes that require post processing to remove.
SLS and SLIM are both fast and cost-effective, making them suitable for creating large and complex parts. These techniques can also produce very accurate metal parts, and are particularly well-suited for manufacturing industrial components. However, SLIM and SLS printing can cause surface defects that may need to be smoothed before the part is ready for use.
For a complete, end-to-end solution for your prototyping needs, Raise3D can help you select and operate the best 3d printer for your business. Our team of experts will assess your needs, advise on the right machine for you, and provide ongoing maintenance and support to minimise downtime. We will also handle all your post-printing processing and finishing to create a professional, polished prototype that you can be proud of.
Customised Products
3D printing enables customised products, which are tailored to individual consumers’ needs and preferences. This is possible by modifying dimensions and materials, allowing designers to fine-tune products for better performance, ergonomic fit, and accessibility features. This customization is also cost-effective, as it eliminates the need for costly tooling changes and reduces waste production.
The use of 3D printing in product development provides a quick and cost-effective solution to test and validate the functionality of prototypes, which is a valuable part of the design process. It can be used to develop parts that are too expensive or inconvenient to make by hand, as well as parts that would not be possible to manufacture using traditional methods.
In addition to its use in prototyping, 3D printing is increasingly being used for manufacturing end-use products, such as dental crowns, jigsaw puzzles, medical implants, and surgical guides. The technology is also useful for constructing functional models of buildings and other structures, and even whole houses are being printed, with one example of a fully-printed house being built in Russia in 2016.
3D printers produce items using different technologies, which include sintering (using lasers or electric arcs to melt and fuse solid material together), powder bed fusion (3D printing with plastic or metal materials that have been mixed beforehand), and stereolithography (3D printing using light to curing material in thin layers). These techniques can be combined to create the most effective design for a particular project.
Despite its vast potential, 3D printing is not without its limitations. For instance, a CAD model may require extensive post-processing to achieve the desired result. Moreover, the cost of customizing or printing an item for testing or small-scale production can quickly add up, especially when specialized packaging and expedited transport are involved. However, with the right partner, these challenges can be overcome to provide a wide range of innovative and unique consumer products. This is the future of the global consumer goods industry, and it is made possible by the power of 3D printing. It allows manufacturers to expedite innovation, explore new designs and meet customer demands for personalization.
Additive Manufacturing
Unlike traditional manufacturing methods which shape an object by reduction or subtraction, additive printing shapes it through the addition of layers. This process allows for greater design flexibility, speed and efficiency than traditional manufacturing processes. Engineers with access to in-house 3D printers don’t need to spend time drafting drawings, creating purchase orders and managing the bidding process with multiple vendors.
3D printing is used in industrial production for prototyping, end-use parts, tooling and other applications. Some common applications include automotive, aerospace, consumer electronics, medical devices, and energy technology.
The 3D printing industry has grown rapidly. Many companies have entered the market, including 3D printing service providers and manufacturers of the machines that use the additive manufacturing process. Many of these devices are ‘smart’ and connect to the cloud, allowing manufacturers to store part files digitally and print to any device connected to the network. These printers also collect data throughout the fabrication process, allowing for analysis of performance, material consumption and printing times to optimise printing output.
A large number of printers are based on the stereolithography method, known as vat photopolymerisation. A UV laser shines into a container of ultraviolet-sensitive photopolymer resin, which hardens to form the model. Some of the newer machines are able to build structures of different sizes, shapes and colours simultaneously. These multi-material machines allow for a wider range of printing materials, such as metals and ceramics.
Another type of printer is the fused deposition modelling (FDM) machine, which heats plastic filament to solidify it into place. This process is quick and relatively inexpensive for small batch production of components. The resulting parts are relatively strong and durable, although they may not be suitable for some applications.
Other 3D printers use a technique called selective laser sintering to build objects from powdered materials, such as aluminium titanium and polycarbonate. These printers are typically slower and more costly than FDM devices.
Despite the rapid growth of the industry, there are still several barriers to widespread adoption of additive manufacturing. First and foremost, it can be expensive for a company to invest in an in-house printer. It is also necessary to invest in the development of post-processing and finishing techniques, which can increase dimensional accuracy and improve surface finish.
Medical Technology
The medical sector is using 3d printing in a variety of ways. Doctors are able to make exact replicas of parts of the body to help plan operations and aid in diagnosis, as well as printing replacement parts for prosthetic limbs, dental crowns and bridges, and hearing aids. The technology is also being used in drug development, as it makes it easier to create precise dosage forms of medication. This can improve efficacy and reduce side effects for patients.
To create medical 3d printed models, doctors must first digitalize a patient’s real anatomical structure by scanning the patient with a CT scan or an MRI. A process called segmentation then takes place to label structures of interest and convert them to a 3D computer model for printing. This can be done manually, but software programs that are designed for this purpose have been developed to expedite the process.
Once the medical model is made, surgeons can practice on it to familiarize themselves with the anatomy of a patient. This can help them avoid complications and shorten surgical time, which can lead to a reduction in postoperative hospital stay, blood loss, and overall cost. In fact, a 2020 study reported that surgeons who used printed anatomical models as guides during surgery reduced their operating time by 62 minutes.
More and more hospitals are installing centralized point-of-care printing facilities to allow physicians to quickly create needed medical items as they treat patients. This can help reduce the need for large inventories and cut costs. Additionally, the speed of printing allows for adjustments to be made promptly based on surgeon feedback.
3D printing can also be used to make custom trays for holding pills and other liquid medications, which can make them easier for patients to swallow and more effective at dissolving in the stomach. This has already been tested on a few medications and is expected to be widely adopted in the future, as it can reduce adverse reactions in certain patients.
Although a few 3D-printed healthcare items have been approved by the FDA, they must go through the same rigorous review process as conventionally made medical equipment to ensure safety and effectiveness. This includes testing the materials to ensure they are biocompatible, durable, and sterile. Most commonly, these are medical-grade polymers like PEEK or ULTEM, which are known for their strength and resistance to high temperatures. Nylon and thermoplastic elastomer (TPE) are other common choices.